Construire son bateau dans son jardin…Voila le résultat !
[ad_1]
La plupart des projets de bricolage sont un peu difficiles sur les bords, mais lorsque Jimmy Callow a décidé de se construire un nouveau bateau, seul le meilleur ferait
J’ai vu quelques bateaux construits à la maison dans mon temps et alors que je suis impressionné par tous ceux qui parviennent à terminer un projet de cette complexité, si vous regardez de près, le résultat final est souvent un peu rude sur les bords. Ce n’est guère surprenant quand on regarde ce qui entre dans la construction d’un bateau.
Cela nécessite tellement de compétences différentes, de la conception à la plomberie, au travail du bois, au génie électrique et mécanique, qu’il est presque impossible pour une seule personne de tout faire. Même si par miracle vous avez les bonnes compétences, vous n’avez toujours qu’une seule chance de le faire plutôt que de perfectionner vos compétences au fil du temps sur une ligne de production.
Donc, quand j’ai entendu qu’un type appelé Jimmy Callow s’était construit un bateau à fly de 44 pieds à partir de zéro, j’ai envisagé une caravane flottante avec un intérieur de base renversé dans son jardin. Jusqu’à ce que je voie les photos. Il avait non seulement l’air de la pièce avec un extérieur élégant et contemporain, mais il était propulsé par une paire de moteurs Volvo D6 et semblait avoir un intérieur qui aurait pu sortir tout droit d’un Fairline ou d’un Princess. Cela nécessitait une enquête plus approfondie.
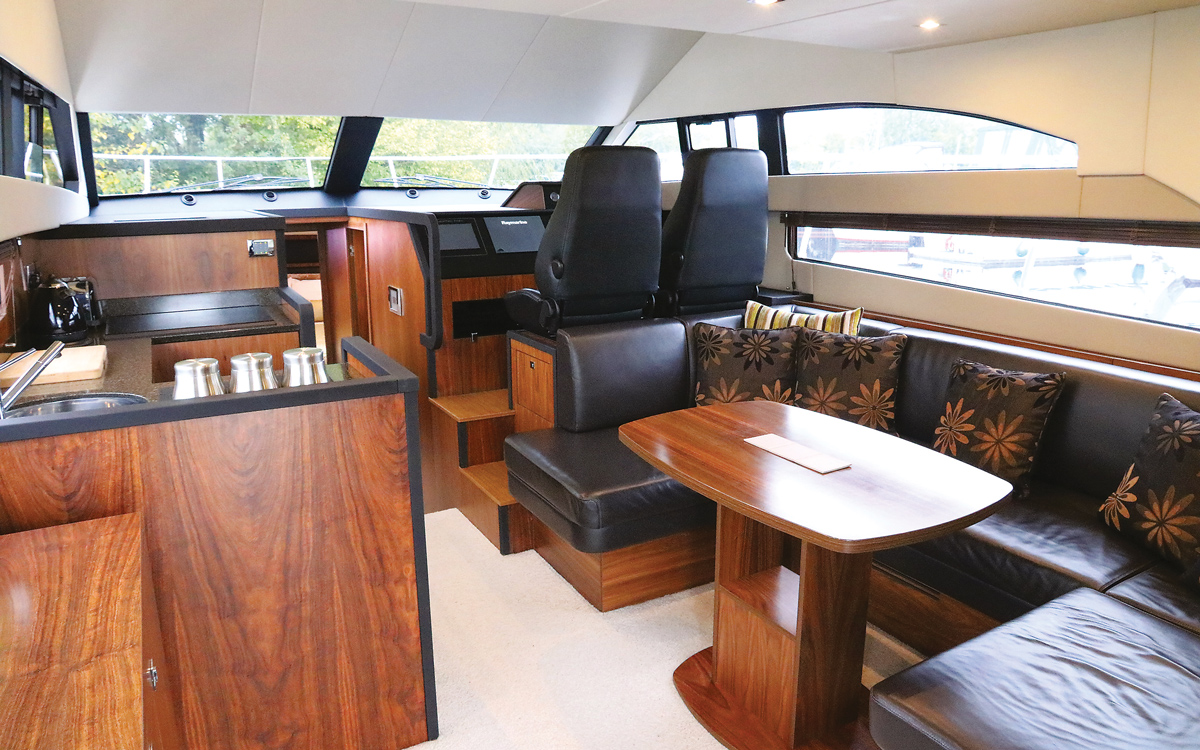
Avance rapide de quelques semaines et je suis assis avec Jimmy sur son bateau dans la marina de Bray près de Windsor. La caméra ne mentait pas. Dans la chair, il ressemble vraiment à un bateau de production moderne avec un éclairage LED, des commandes d’écran tactile sur mesure et des accessoires design de haute qualité.
Il a même sa propre marque avec le nom de la marque et du modèle arborant fièrement le long de la superstructure – Fabritec F44. S’il était exposé dans un salon nautique, vous supposeriez tout naturellement qu’il venait de sortir d’une chaîne de production – et non pas d’un volume élevé et à bas prix non plus. C’est vraiment bon. Alors, comment l’a-t-il fait?
L’histoire commence en 1988, lorsque Jimmy avait 19 ans. Lui et son père ont pris un vieux bateau de croisière de 18 pieds rempli de pluie en échange d’une cuisine qu’ils avaient équipée. C’était un début peu propice mais cela a donné à Jimmy le virus de la navigation de plaisance alors qu’il se promenait autour des rivières et des voies navigables du nord du Kent.
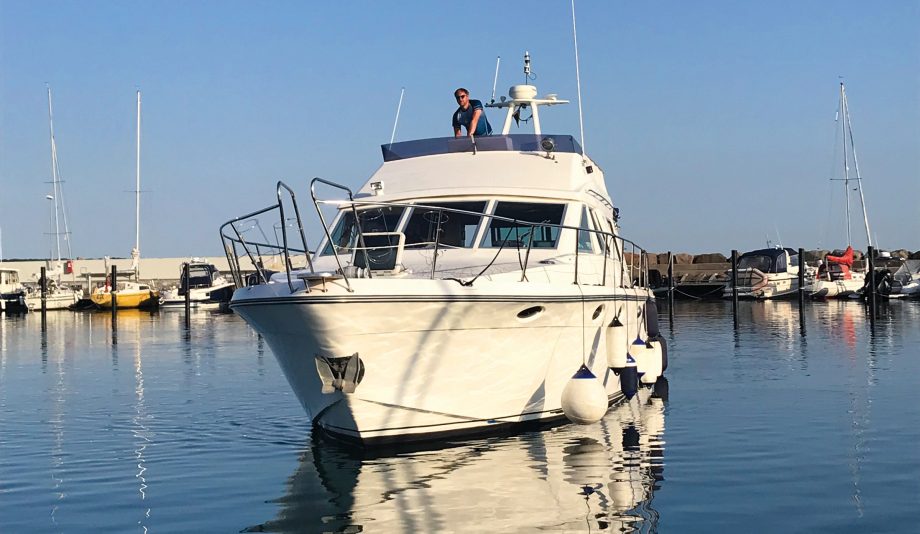
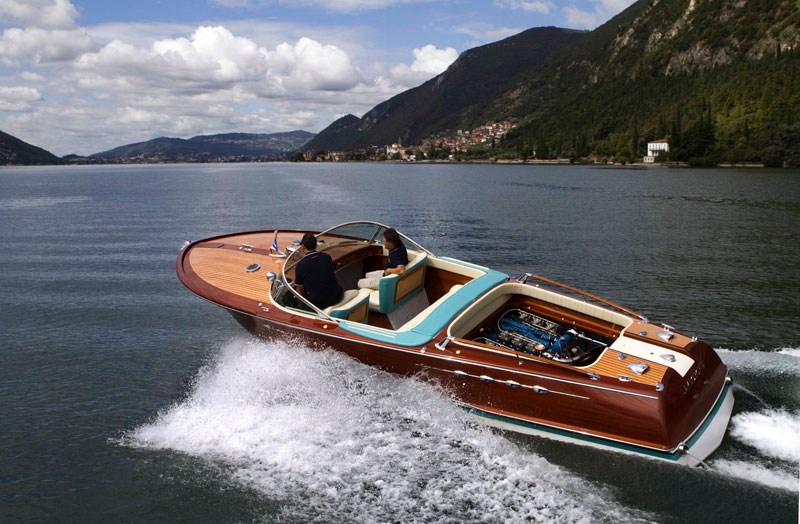
Bateau à moteur et yachting | Riva Aquarama Lamborghini
Riva Aquarama Lamborghini est l’Aquarama le plus rapide jamais construit, capable de 48 nœuds
Peu de temps après, il a commencé à aspirer à quelque chose de plus grand qu’il pourrait rester à bord, mais l’argent était serré et acheter même un bon 30 pieds d’occasion était hors de portée. Puis, en 1994, il est tombé sur un flybridge Colvic Sunquest 34 inachevé qui avait été repris par la banque.
Les moteurs, la direction et l’électricité avaient déjà été installés mais pas l’intérieur, et surtout la banque tenait à s’en faire tirer dessus. Sentant une opportunité, Jimmy l’a saisie. Il avait toujours été bon avec ses mains et diriger une entreprise de fabrication de meubles signifiait qu’il avait accès à la plupart des outils et des matériaux dont il avait besoin pour concevoir et construire son propre intérieur.
Il lui a fallu près de deux ans pour terminer, mais le résultat final a été un bateau familial confortable qui a permis à Jimmy, à sa femme Karen et à ses deux jeunes filles de profiter en famille. Initialement, ils l’ont gardé dans le port de plaisance de Gillingham en l’utilisant comme base à partir de laquelle explorer la Medway et la Tamise avant de décider de le déplacer de façon permanente en amont de la rivière jusqu’à la marina de Bray.
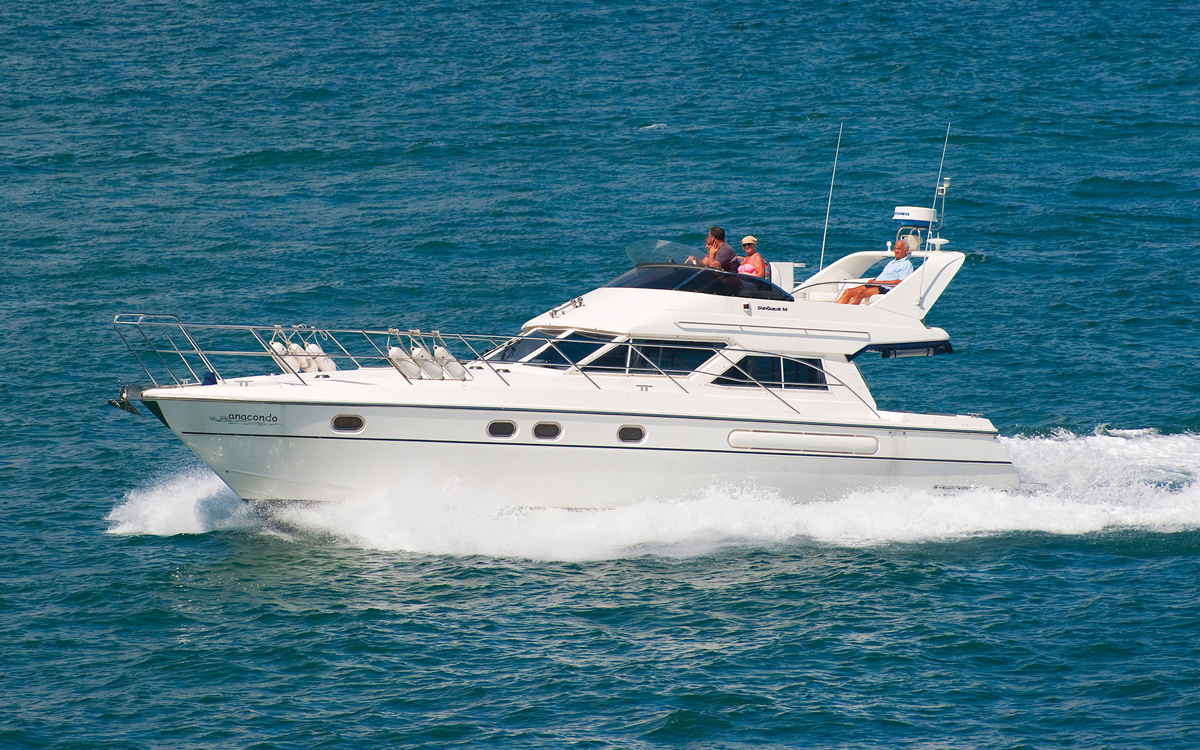
«Sur la côte, nous devions souvent changer nos plans en raison du mauvais temps, mais sur la rivière, nous pouvions profiter d’une saison plus longue et même s’il faisait trop de vent pour la retirer de la marina, nous pouvions toujours rester à bord et l’utiliser comme chalet de fin de semaine », explique Jimmy.
Ils ont gardé le bateau pendant 19 ans mais en 2014, avec leurs filles maintenant à la fin de leur adolescence, le moment est venu de se moderniser à nouveau. «L’espace était restreint et le Colvic devenait de plus en plus difficile à entretenir, si nous devions continuer à naviguer en famille, nous avions besoin de quelque chose de plus grand. C’etait maintenant ou jamais. »
L’achat d’un tout nouveau 40 pieds n’était pas une option, mais Jimmy était déterminé à trouver un remplaçant avec au moins deux cabines de bonne taille et tout le confort moderne dont ils auraient besoin pour les garder en sécurité et à l’aise pendant les 20 prochaines années.
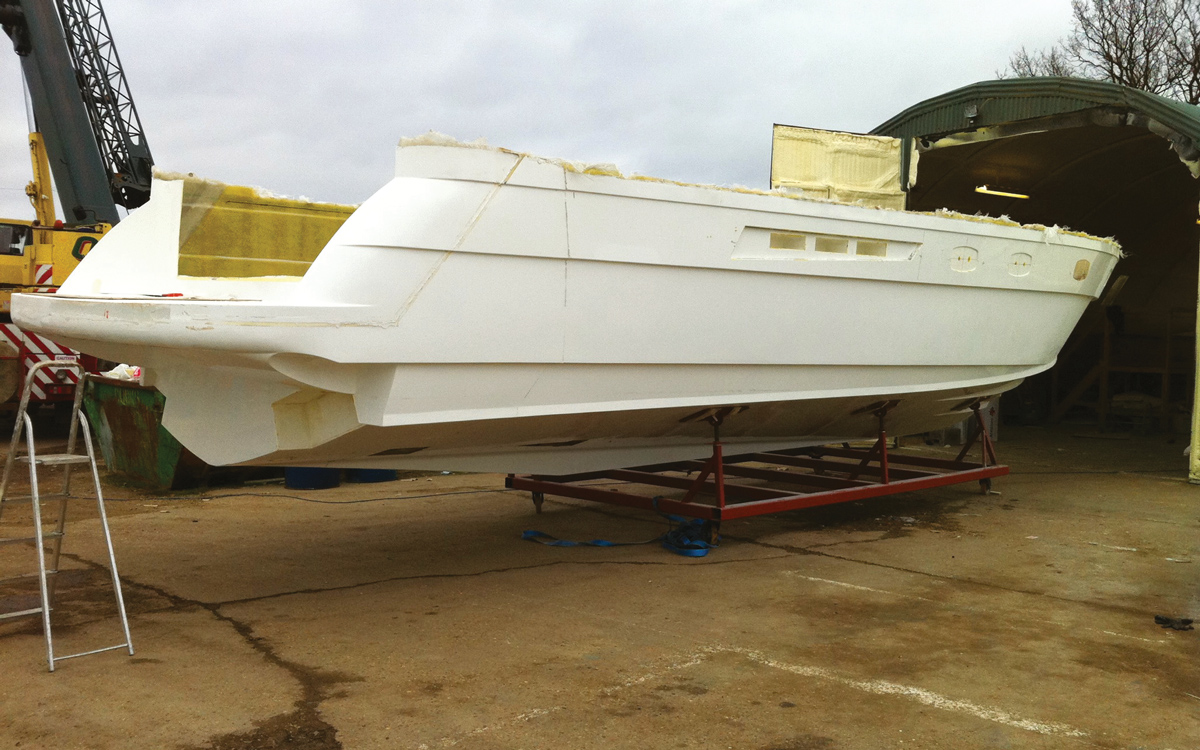
Comme auparavant, il a cherché sur le marché de l’occasion quelque chose de convenable, mais est rapidement arrivé à la conclusion que rien ne convenait parfaitement à son budget. La plupart des passerelles qu’il a examinées étaient conçues pour les climats ensoleillés alors qu’il voulait quelque chose qui était tout aussi confortable par une froide journée d’hiver sur la Tamise.
Cela signifiait des systèmes de chauffage et de climatisation puissants, un générateur à haut rendement pour qu’ils ne dépendent pas de l’alimentation à quai, une cuisine de taille domestique avec beaucoup de stockage et un intérieur pratique mais élégant qui se sentirait comme une vraie maison. Une fois de plus, il a conclu que la construction de son propre bateau pourrait être la seule solution viable au problème.
Monte socialement
«J’ai cherché un point de départ approprié et j’ai rencontré une société appelée Zenon Yachts qui construit des coques Colvic Sunquest 44 pour le marché norvégien. Je savais que le modèle avait une bonne réputation en matière de tenue à la mer car la coque avait été conçue par John Bennett mais certains aspects du style semblaient assez datés. J’ai réfléchi à la manière de le moderniser et j’ai discuté de mes idées avec Zenon Yachts.
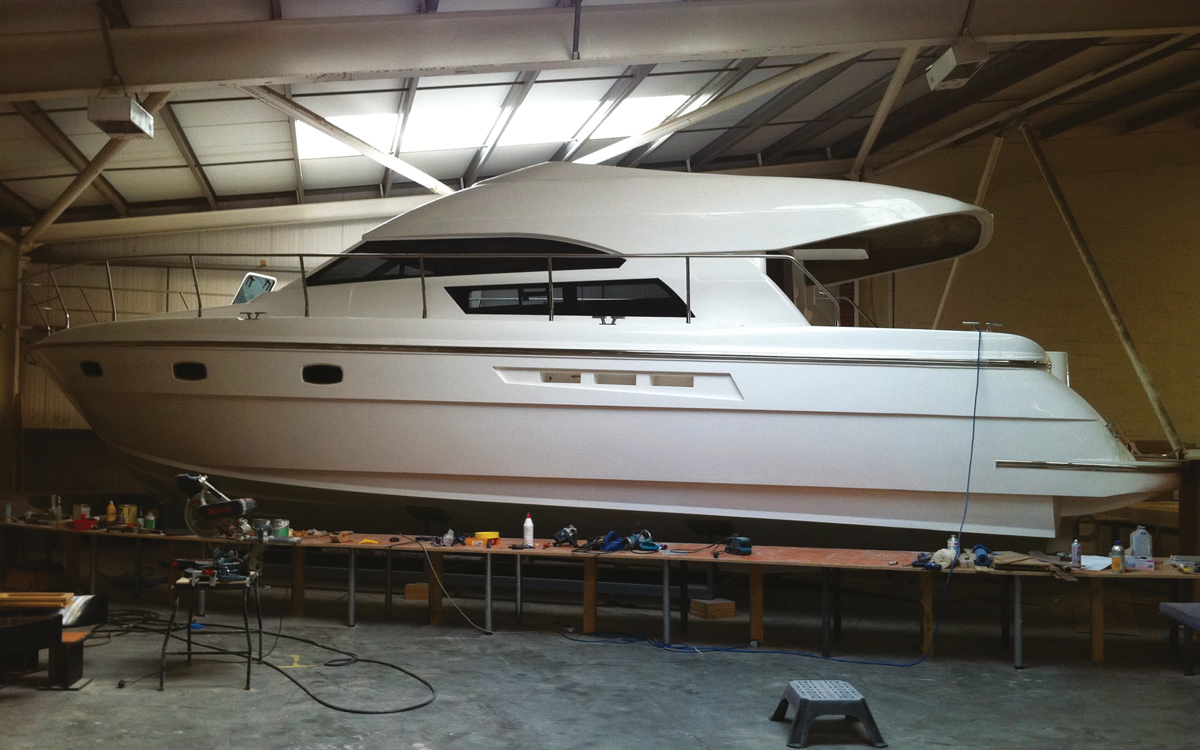
«Nous avons convenu de travailler ensemble pour mettre à jour la conception avec de nouveaux hublots, fenêtres et pare-brise ainsi qu’un nouveau flybridge et un arc radar repliable. Nous avons approché Trend Marine pour fabriquer les fenêtres, qui ont accepté, mais seulement si nous en achetions au moins trois ensembles. Heureusement, Zenon Yachts a réussi à obtenir deux commandes pour le bateau redessiné de Norvège et j’ai accepté d’acheter le troisième. Nous avons modelé les moules existants et fabriqué de nouveaux bouchons et outils pour s’adapter aux fenêtres révisées. »
Zenon s’est mis au travail pour mouler les nouvelles coques et en 2011, la coque nue et la superstructure ont été livrées à l’usine de Jimmy, FabriTec Furniture Ltd, à l’arrière d’un camion où il avait déjà construit un berceau roulant pour le faire rouler à l’intérieur de l’atelier. Il a payé 60000 £ pour les moulures, mais contrairement à son projet précédent, le reste était complètement nu: pas de moteurs, pas d’électricité, pas de poupe, pas de plomberie, pas d’intérieur – juste une coque de fibre de verre vide.
«Il y avait toujours des choses qui n’allaient pas tout à fait avec notre précédent bateau. J’ai donc dit que si je recommençais, je construirais tout le bateau à partir de zéro. C’était ma chance. »
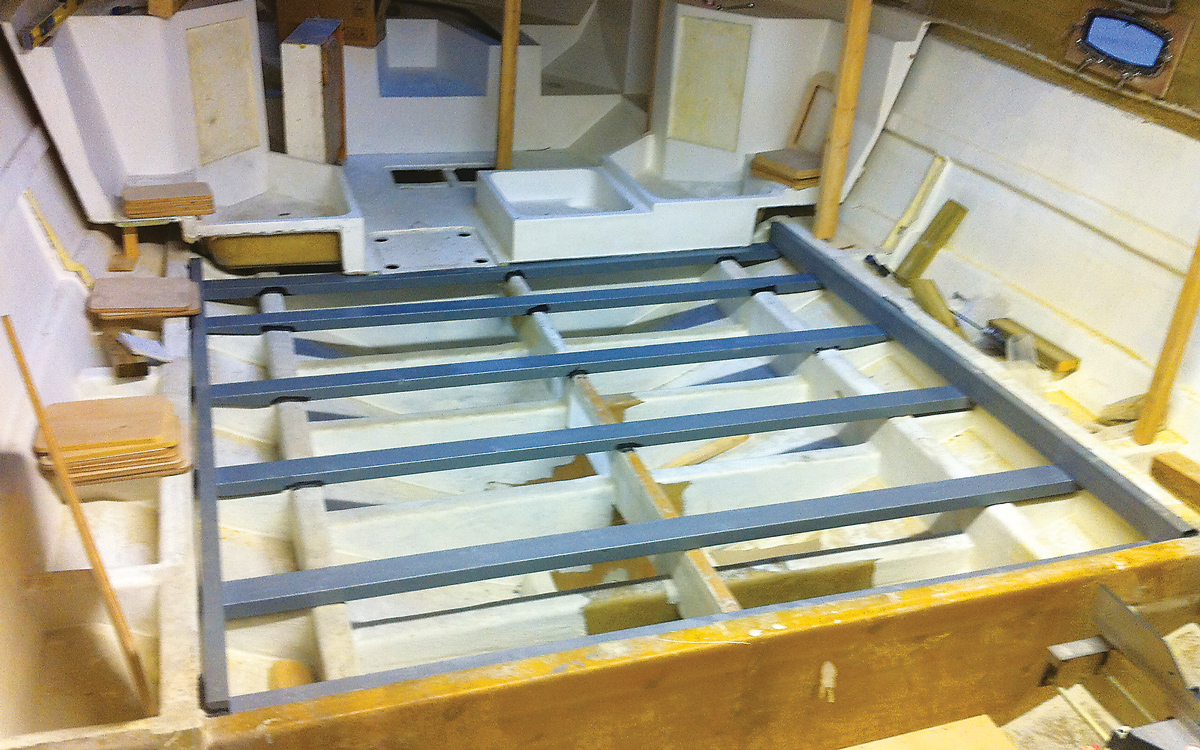
Son premier défi a été de concevoir et d’adapter un ensemble de garde-corps et de cadres de verrière en acier inoxydable, mais plutôt que de les sous-traiter à un fabricant de métaux, il a acheté du matériel de cintrage d’acier et a appris lui-même à façonner les tubes pour s’adapter à ses nouveaux modèles. « Papa m’a toujours appris que si quelqu’un d’autre peut le faire, vous aussi – j’ai grandi avec cette philosophie, donc apprendre une nouvelle compétence ne me déconcerte pas. »
Il a fait appel à un soudeur spécialisé pour s’assurer que les joints étaient propres et solides, mais à part, il a dessiné, façonné, assemblé et installé un ensemble complet de mains courantes pour son nouveau bateau.
Le travail de l’acier inoxydable terminé, Jimmy s’est tourné vers le montage des fenêtres et des hublots Trend Marine. Contrairement aux fenêtres à cadre en aluminium du Colvic Sunquest 44 d’origine, il s’agissait de conceptions sans cadre affleurantes qui nécessitaient que Jimmy apprenne une autre compétence pour les ajuster et les sceller correctement.
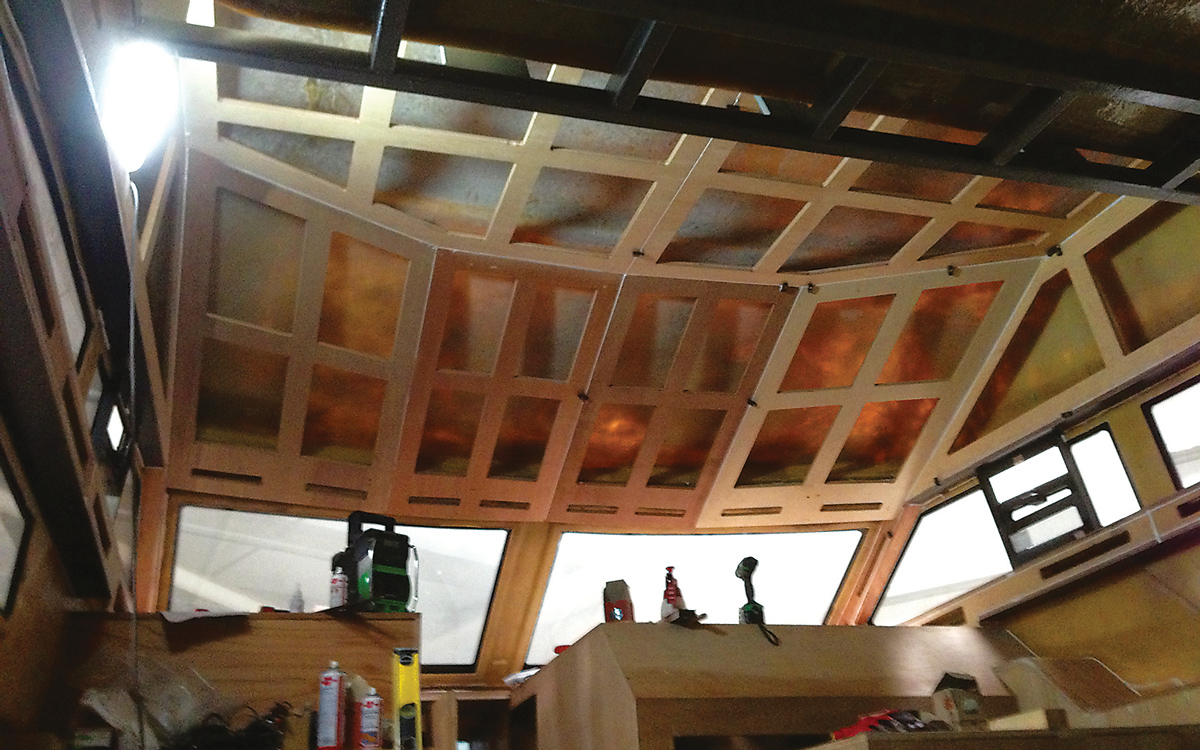
Strict nécessaire
Suivant sur la liste étaient les moteurs et les sterngear. Jimmy souhaitait installer Volvos en raison du réseau mondial d’agents de maintenance et a d’abord envisagé de monter une paire de D6 de 370 ch avant de choisir les variantes plus puissantes de 435 ch, qu’il a achetées auprès de Coastal Rides à Douvres.
Il voulait la simplicité des arbres plutôt que des IPS ou des sterndrives même si cela signifiait concevoir et construire ses propres supports et supports de moteur qui s’aligneraient précisément avec les arbres et les supports en P. Heureusement, sa connaissance de la CAO (conception assistée par ordinateur) lui a permis de concevoir et de vérifier trois fois toutes ses mesures avant de s’engager sur quoi que ce soit.
Au cours de la construction, Jimmy estime qu’il a réalisé plus de 2500 dessins CAO et a passé plus de 2500 heures sur la recherche et la conception uniquement. Cela, insiste-t-il, est la clé de la précision et de la qualité du bateau fini, et a finalement permis d’économiser beaucoup plus d’heures et de dépenses que de se fier aux essais et aux erreurs pour faire les choses correctement.
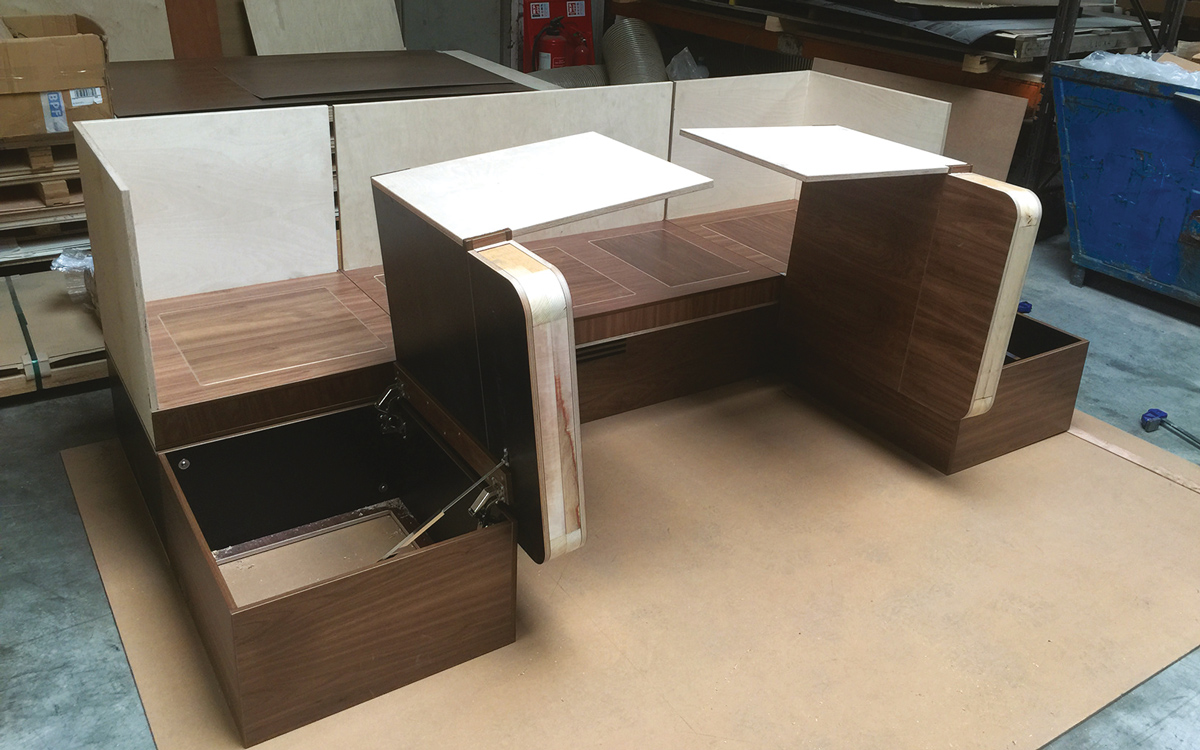
Effectivement, les moteurs et les arbres se sont parfaitement insérés, permettant à Jimmy de passer à l’aménagement intérieur. À bien des égards, c’était la partie la plus difficile à craquer, non seulement parce que c’est la partie de la construction qu’elle est exposée en permanence, mais aussi parce qu’elle impliquait de trouver tous les bons accessoires et matériaux pour s’assurer qu’elle ressemblait à la pièce et résistait à l’épreuve du temps.
Avant de commencer à travailler dessus, lui et Karen sont allés à chaque salon nautique sur lequel ils pouvaient chercher de l’inspiration et des idées sur lesquelles s’appuyer pour leur nouveau bateau, en tirant des tapis, en ouvrant des tiroirs et en vérifiant les noms des fournisseurs. Parfois, Karen montait la garde près du cockpit tandis que Jimmy s’enfonçait à l’intérieur, à d’autres occasions, ils expliquaient simplement ce qu’ils faisaient et demandaient même des conseils si le concepteur ou les constructeurs étaient à portée de main.
Fièvre de cabine
Sans cloisons internes installées, leur premier travail a été de concevoir un agencement adapté à leurs besoins, mais également de créer un cadre interne solide pour soutenir la coque et la superstructure – les coques en GRP sont intrinsèquement flexibles sans un.

Les 44 originaux avaient une disposition de cuisine avec deux cabines doubles, mais Jimmy et Karen ont décidé de monter la cuisine dans le salon et d’utiliser l’espace ci-dessous pour une troisième cabine superposée. Avec la disposition convenue, Jimmy a conçu et construit un cadre structurel complet de supports, de poutres de pont, de cloisons et de panneaux avec une isolation supplémentaire pour le garder au chaud en hiver. « C’est probablement un peu exagéré », admet Jimmy. « Mais je voulais être sûr que c’était sûr. »
La structure terminée, il se mit au travail de planification et d’installation des systèmes électriques nécessaires à l’alimentation du bateau. Les blocs de construction de celui-ci ont été conçus et fournis par Energy Solutions à l’aide d’un générateur Fischer Panda de 10 KVA avec six batteries domestiques et deux pour les démarreurs de moteur. Une fois de plus, Jimmy a lui-même installé tous les câblages et tableaux ainsi que l’éclairage LED, les propulseurs d’étrave et de poupe.
Le prochain sur la liste était la cuisine et le salon. «Karen voulait une plaque à induction à quatre feux et un four ainsi qu’un réfrigérateur domestique de grande taille. Ils sont tous fabriqués par Bosch et montés par mes soins. »
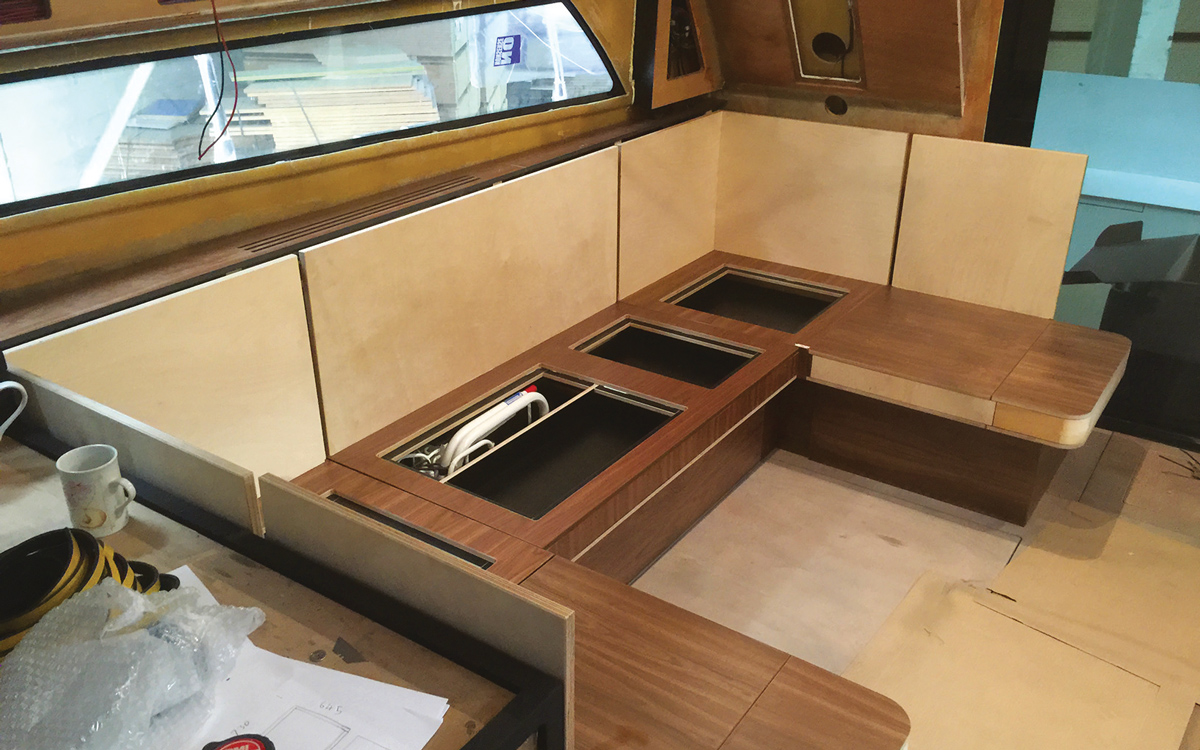
Cependant, ce n’est pas seulement l’équipement qui regarde la pièce, les surfaces de travail sont toutes en Corian tandis que les remparts à mi-hauteur qui agissent à la fois comme entrée de la cuisine et comme poignées pour les invités qui avancent sont surmontés de barres d’appui à section rectangulaire recouvertes de un revêtement doux au toucher effet mat.
«J’ai volé cette idée à un Fairline Squadron 42», admet Jimmy. «J’ai fabriqué les garde-corps en contreplaqué, puis j’ai trouvé les gars qui ont fourni le revêtement à Fairline et je les ai pulvérisés avec les mêmes produits.»
Le siège du salon, quant à lui, a été conçu autour du système de climatisation Eberspächer afin de le garder hors de vue mais toujours facilement accessible pour l’entretien. Les bases articulées dans les retours latéraux créent un stockage supplémentaire et le tout a été simulé en carton puis fabriqué dans l’usine FabriTec avant d’être installé sur le bateau. Bien qu’il utilise des placages en bois véritable, ils ont été recouverts d’une finition en mélamine qui ne se décolore pas ni ne s’use.
La cuisine comprend des appareils électroménagers Bosch de qualité supérieure.
«Cela nous a presque coûté notre mariage», admet Jimmy en plaisantant à moitié. «Il y a eu des moments où j’ai voulu tout rentrer et revenir à la vie normale, mais nous sommes restés avec et cela a décuplé ce que nous y avons mis.»
Ce n’était pas non plus une entreprise bon marché. Tout cela lui a coûté 220 000 £ à construire, même sans tenir compte des milliers d’heures de travail que Jimmy y a consacrées. Il est difficile de dire ce que cela peut valoir maintenant, mais Jimmy l’a fait officiellement évaluer à des fins d’assurance en 2015 à 450 000 £. Plus important encore, de son point de vue, essayer de trouver un nouveau bateau avec trois cabines et toutes les spécifications qu’il voulait lui aurait coûté plus de 650 000 £.
Enfin, en 2015, le moment est venu de lancer leur nouveau bateau. Comme avant, ils ont choisi Gillingham Marina et ont attendu avec impatience le moment où elle a été descendue dans l’eau et baptisée Anna Mae après leurs filles Ellie Mae et Alix Anna. Après une vérification rapide pour s’assurer qu’il n’y avait pas de fuite et deux semaines de mise en service finale, Jimmy a pris des dispositions pour qu’un agent Volvo agréé l’accompagne dans les essais en mer officiels nécessaires pour valider la garantie des moteurs.
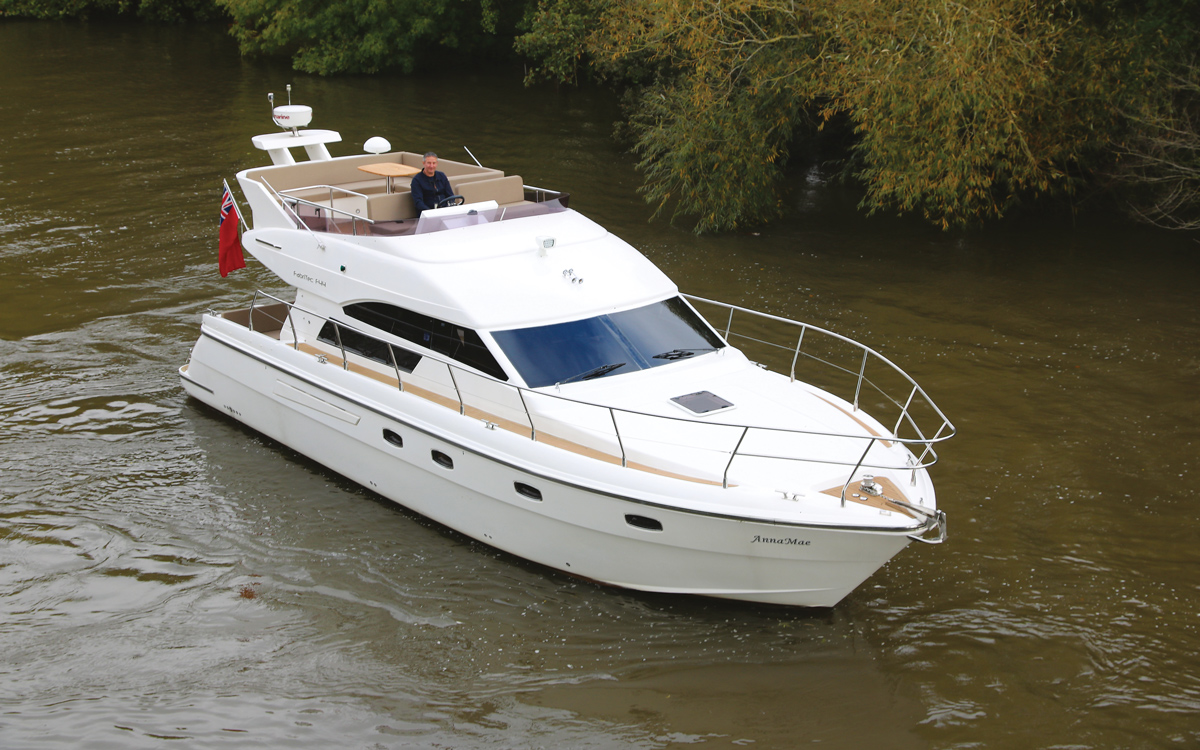
«Après avoir branché leurs ordinateurs et m’avoir demandé d’augmenter le régime de 500 tours à la fois, le bateau a commencé à prendre de la vitesse. Je n’arrêtais pas de leur dire que je devais ralentir car il y avait un voilier à proximité, mais il m’a juste dit: « continuez pas, continuez! » Nous avons atteint 30 nœuds à plat puis avons dû tout recommencer en ouvrant les gaz entièrement à partir d’un départ arrêté pour mesurer l’accélération. Nous avons atteint 30 nœuds en 20 secondes. Elle est passée avec brio. »
Heureux jusqu’à la fin des temps
Depuis ce baptême du feu en 2015, Jimmy et Karen ont déménagé Anna Mae retour à la Tamise. Ils passent un week-end sur elle au cours des mois d’été à se rendre à Abingdon ou à l’estuaire de la Tamise avec des incursions occasionnelles plus longues le long de la côte pour dégager la gorge des moteurs.
L’objectif à plus long terme est de réduire progressivement leurs engagements professionnels et d’utiliser le temps pour naviguer plus loin vers Paris, la Baltique et, éventuellement, les climats plus chauds de la Méditerranée. « Il n’y a aucun moyen que nous aurions pu nous offrir un bateau comme celui-ci si nous ne l’avions pas construit nous-mêmes », explique Jimmy avec nostalgie. « Je dois encore me pincer pour dire qu’il nous appartient réellement. »
Après quatre ans, 5 000 heures et 220 000 £, je pense qu’ils ont gagné le droit de l’appeler le leur!
Coûts et fournisseurs
Moulures de coque et de superstructure: Zenon Yachts – 50 000 £
Sièges, barre et arceau radar: Bricolage – 6000 £
Mains courantes: Bricolage – 3800 £
Fenêtre et porte patio: Trend Marine – 7 000 £
Système électrique et générateur: Solutions énergétiques – 36 000 £
Chauffage et climatisation Webasto: Keto Ltd – £12,500
Raymarine nav gear: PSI Marine – £12,500
Twin 435hp Volvo D6 engines: Coastalrides – £60,000 (inc. installation)
Seating upholstery: Quayside & Leisure – £8,000
Other materials & fittings: Various – £25,000
Coût total: £220,800
Labour hours
Research, design & CAD drawing: 2500
Handrails: 120
Les fenêtres: 40
Bulkheads & superstructure: 480
Plumbing & heating: 160
Wiring: 800
Furniture & fittings: 500
Radar arch & seating: 250
Engine & sterngear: 150
Total: 5,000 man hours
[ad_2]