Comment nous avons conçu et construit un dériveur pliant pour moins de 350 €
[ad_1]
Gordon Davies et Alison Mainwood décrivent comment les essais et erreurs les ont conduits à concevoir et à construire leur propre dériveur compact et très léger à un prix très raisonnable.
Un dériveur ajoute énormément de plaisir à des vacances en croisière, mais sur un petit bateau, il y a toujours le problème de savoir où le ranger.
Accrochez-le sur des bossoirs et il gêne les manœuvres serrées et peut bloquer la vue vers l’arrière; le ranger sur le pont est souvent une nuisance.
Notre premier yacht était un Moody 31 d’occasion, qui était livré avec un pneumatique et un hors-bord Avon soignés. Nous pouvions le ranger en dessous et le gonfler rapidement, mais nous détestions la gymnastique impliquée dans le montage du hors-bord et n’aimions pas transporter de l’essence.
En élaborant notre style de croisière, nous avons réalisé que nous avions rarement besoin du moteur. Dans un mouillage paisible, il était préférable de ramer tranquillement, et notre dériveur ramait aussi mal que la plupart des structures gonflables.
Le bien-aimé Moody était notre week-end et maison de vacances pendant huit ans et c’était le dériveur que nous avions.
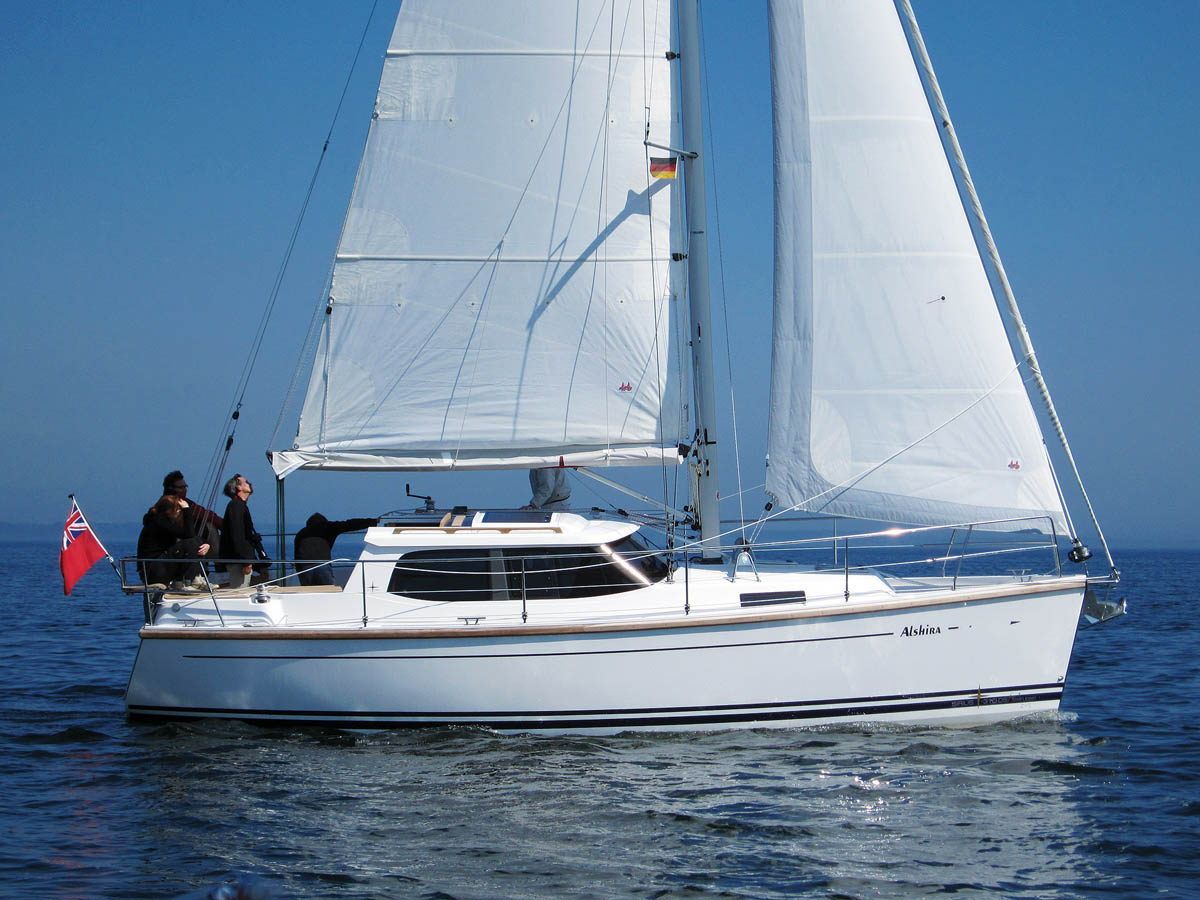
Sirius 310 Alshira La flèche autovireuse signifie que le rangement du pont avant pour une annexe est hors de question
Gordon a pris sa retraite en 2010 et nous avons fait construire notre bateau de salon de pont Sirius 310. Alison travaillait toujours, alors nous avons gardé Alshira à la base du constructeur dans le nord de l’Allemagne pendant un été et j’ai appris à la connaître.
Alison adorait pouvoir voir dehors pendant qu’elle naviguait, et un retour pénible sur le canal de Kiel sous une pluie battante a montré l’avantage du poste de pilotage intérieur.
Nous aimions pouvoir faire les passages plus longs avec nous deux à l’intérieur, au chaud et au sec.
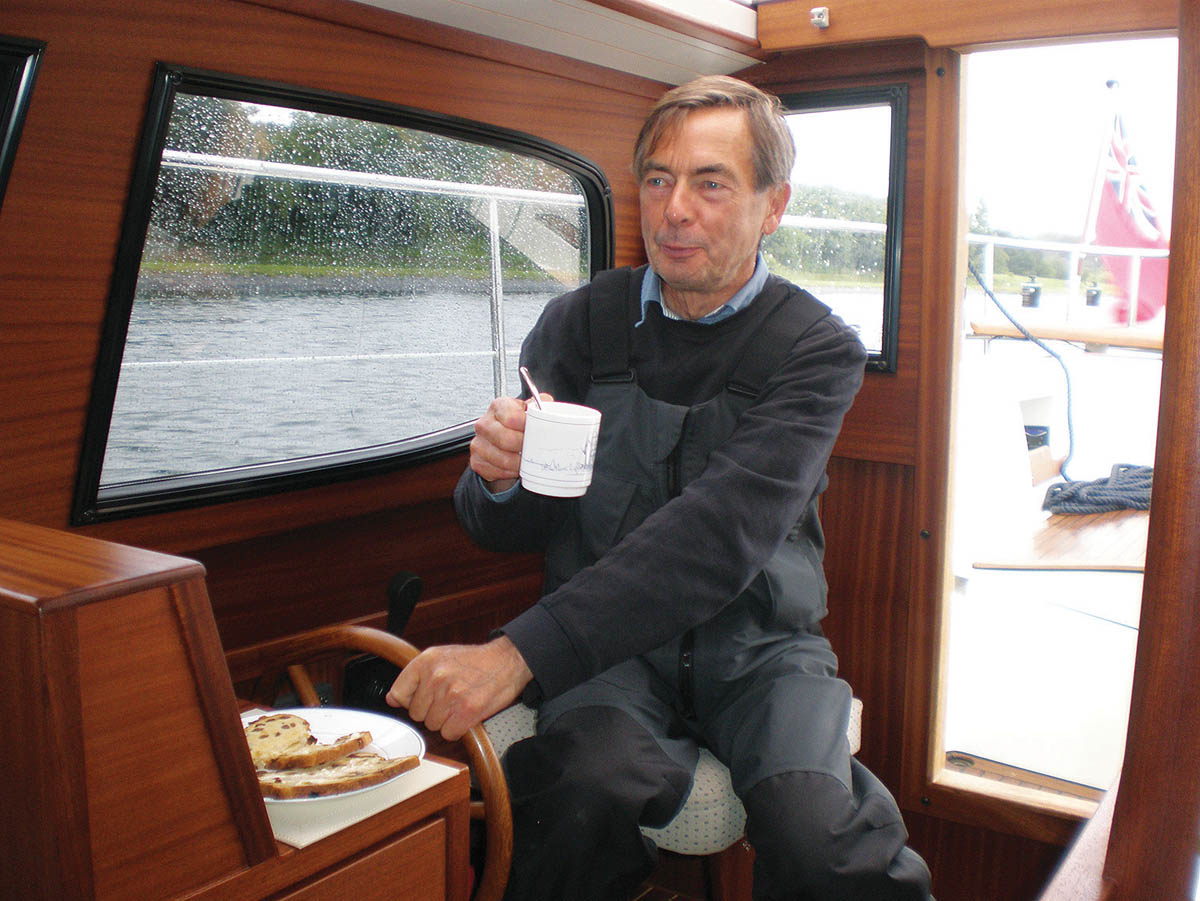
La visibilité depuis la position de barre intérieure peut être facilement bloquée par des engins attachés aux chandeliers
La vision à 360 ° était essentielle. Et cela a créé un problème pour le rangement des canots pneumatiques sur le pont.
Il y avait d’excellents modèles de dériveurs pliants commerciaux et des annexes de nidification sur le marché, tels que le Banana Boat et le Portaboat, mais les versions adaptées pour deux adultes se rangent sur toute la longueur (plus de 2,5 m), elles devraient donc être attachées aux chandeliers bloquant notre point de vue. Nous avons un foc autovireur et ne pouvons donc pas transporter quelque chose comme un Nestaway sur le pont avant.
Nous étions également à la limite de notre budget nautique.
Mais il y avait une solution simple qui nous plaisait. Étant donné que nous avons une vaste expérience dans la fabrication de kayaks en contreplaqué, pourquoi n’avons-nous pas fabriqué un dériveur pliant en contreplaqué, conçu pour le stockage dans le local technique?
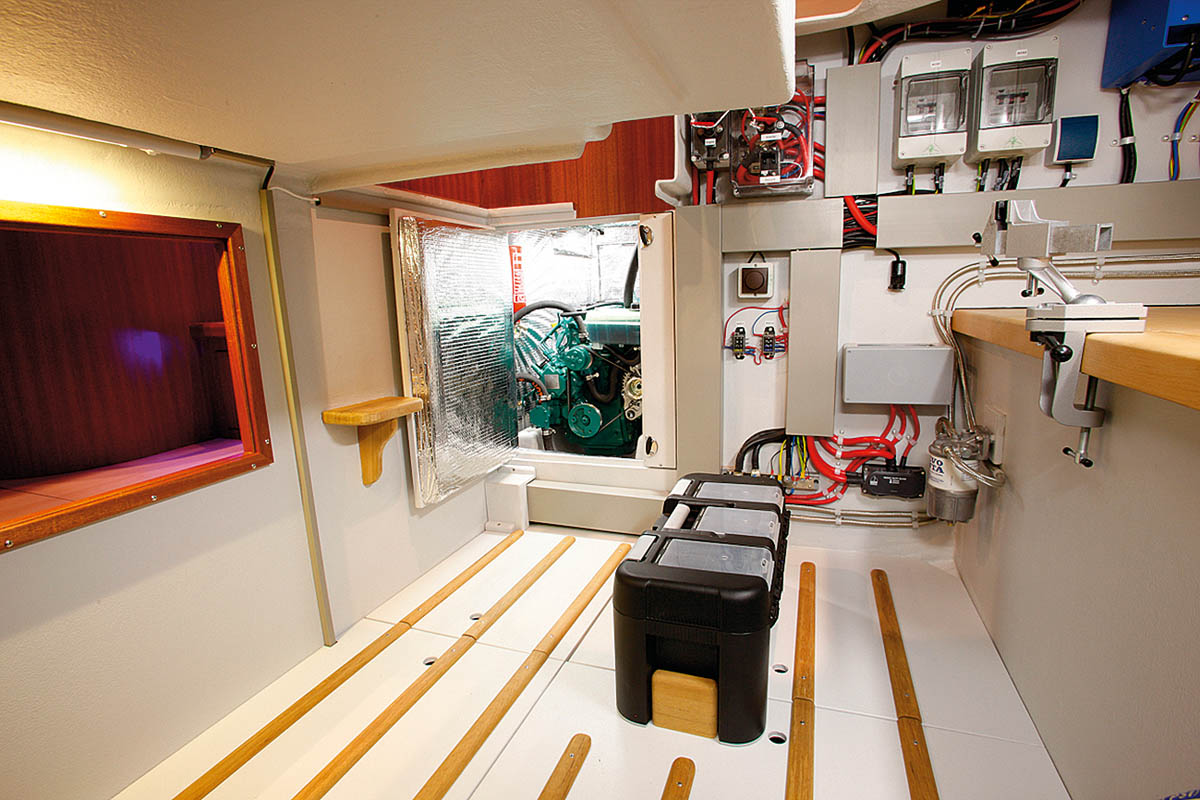
A bord du salon de pont Sirius 310 – nous avions spécifié un local technique au lieu d’une cabine sous le cockpit (photo de David Harding)
Nous n’avons de visiteurs qu’occasionnellement et une cabine sur le Moody avait toujours été «le hangar». Sur notre nouveau bateau, nous avons choisi de n’avoir qu’une seule cabine. En plus de nous offrir une cabine et un compartiment de tête beaucoup plus grands, nous disposions désormais d’un local technique sous le carré surélevé.
Eh bien, ce n’est pas si simple que ça…
Dans les jours précédant les dériveurs gonflables, il était courant d’avoir un dériveur dur, d’être laissé sur le mouillage…
Un dériveur de 2,7 m avec un plancher en aluminium solide est génial, jusqu’à ce qu’il vienne à le déplacer sur terre -…
J’ai vu pour la première fois un bateau à berceau lors d’un salon de bateaux en bois il y a des années et je me suis dit: «Quand j’ai des enfants,…
Comment concevoir un dériveur pliant
Avant de couper du bois, nous avions besoin d’un design précis, mais c’était l’idée d’Alison de créer un modèle qui nous a aidés à réaliser un certain nombre de caractéristiques importantes du concept.
1. Chaque panneau latéral est joint à son panneau inférieur tout le long du bouchain. Lorsque le bateau est plié, le panneau latéral repose à plat sur le panneau inférieur, ce qui ne peut se produire que si les bords incurvés adjacents ont exactement la même forme.
2. Ce premier point veut que lorsque le dériveur est déplié, le panneau inférieur se plie à la proue et à la poupe, créant un balancier, ou une courbure, sur le dessous du bateau.
3. La quantité de bascule dépend de l’inclinaison des côtés.
4. Le plat-bord n’est pas une simple courbe grâce à la quantité de bascule et aux différents angles des panneaux lorsque le bateau est déplié.Comment fabriquer ses propres rames
Nos tiges d’aviron n’ont pas la section transversale circulaire habituelle – une forme elliptique économise du poids et est tout aussi solide dans le sens de la traction.
Il y a longtemps, nous avons décidé qu’il était préférable d’utiliser une serrure en métal plutôt qu’une goupille en bois. Nous utilisons une cheville à travers l’arbre et un coussin de corde pour empêcher l’aviron de glisser à travers le rowlock.
Les lames des rames ont été fabriquées en stratifiant trois couches de nappe marine de 3,8 mm forcées en forme de cuvette par un assemblage de pinces. La lame est collée dans une fente de la tige.
Première tentative de construction d’un dériveur pliant
Le local technique sur Alshira mesure 1,8 m de long et nous avons donc estimé que le dériveur ne devrait pas dépasser 1,4 m.
Cela nous donnerait toujours une offre utilisable.
À la recherche d’idées, nous avons été impressionnés par la Conception de Flapdoodle. C’était trop grand pour nous mais nous a donné des idées précieuses.
Nous avons commencé à construire pendant l’hiver froid de 2010 – trop froid pour utiliser le garage pour la construction, donc la chambre d’amis est devenue la station de vernissage et le salon était le chantier naval.
La forme de base de cette première tentative a été un succès, et nous l’avons conservée à travers des builds successifs:
- Le bateau avait un seul échine. Chaque côté pourrait être plié vers l’intérieur sur le dessus de la planche inférieure.
- La bande centrale étroite permettait aux deux moitiés du bateau de se plier ensemble pour donner un emballage qui pouvait être transporté sous le bras.
- Nous avons découpé les panneaux de la coque en pli de 6 mm et les avons cousus avec une ligne de pêche en nylon.
- Les joints ont été scellés avec un tissu enduit de plastique, maintenu fermement aux panneaux en vissant des bandes de pli de 6 mm sur leurs bords.
- Le tissu recouvrait la proue et la poupe, avec des panneaux de pli de 6 mm fendus derrière eux.
- Les sièges étaient pli de 10 mm pour plus de solidité.
- Les boiseries avaient l’air bien et le bateau était incroyablement solide.
Mais la force est venue au prix du poids – une grande partie de la coque était une double épaisseur de pli de 6 mm – et pire encore, elle a coulé. Nous n’avons jamais pu rendre les extrémités du bateau complètement étanches. Donc finalement nous avons abandonné et avons recommencé.
Un dériveur pliant Mark II
Il était essentiel de réduire le poids, nous sommes donc passés au pli de 4 mm et les vis ont été interdites. Nous devions verrouiller tous les composants ensemble. Ce qui a suivi est appelé diplomatiquement une courbe d’apprentissage abrupte, mais nous avons bien compris.
Cette conception utilisait une poutre transversale. Pour l’empêcher de sauter de son support, nous l’avons simplement épinglé avec un morceau de cheville de 6 mm – une queue de queue ou un trennel – qui fonctionnait parfaitement. Le goujon est faible lorsqu’il est plié mais résiste fortement au cisaillement.
Sur ce bateau, nous avons collé du tissu imperméable sur les panneaux latéraux et inférieurs et avons continué le tissu autour des arcs et de la poupe.
Mais encore une fois, cela n’a pas fonctionné. Le tissu s’adaptait parfaitement au bateau plié, mais il était ample lorsque le bateau était déplié et était donc vulnérable à l’abrasion.
Les coutures en nylon frottaient également contre le matériau lorsque les joints étaient pliés et dépliés. Et il y avait toujours le problème des fuites aux extrémités des bouchons que nous ne pourrions jamais résoudre.
Mais nous avions maintenant un dériveur léger qui pouvait nous transporter tous les deux. Il était un peu confortable, avait l’air ridiculement petit, mais était de taille similaire à notre gonflable Avon original pour deux personnes.
Mais nous pourrions sûrement améliorer la conception pour qu’elle ne fuit pas…?
Troisième fois chanceux!
En 2012, Alison a pris sa retraite et nous sommes partis pour le premier de nos voyages d’été de plus de quatre mois, ce qui nous a donné le temps de réfléchir.
Pour faciliter l’aviron et plus de sécurité, il serait bon d’avoir un bateau plus grand, d’environ 2,5 m de long.
Pour le rangement qui nécessiterait une nouvelle conception permettant au bateau de se diviser en deux.
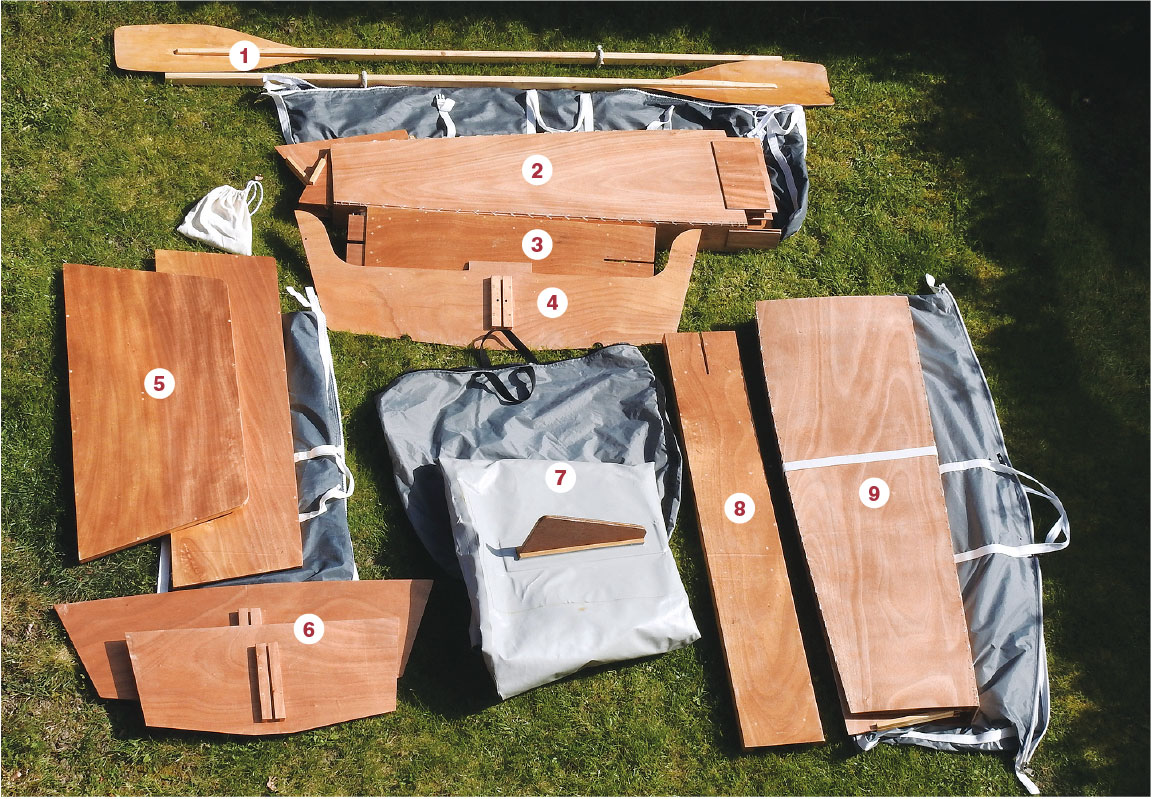
Les deux sections principales de la coque mesurent environ 1,25 m de long et ont chacune un sac. Les sièges et la cloison pleine largeur entrent également dans ces sacs. Le troisième sac contient les sections avant et arrière et les ponts, tandis que le quatrième est destiné à la peau étanche. 1. Avirons 2. Sections de coque avant 3. Moitié avant du siège longitudinal 4. Cloison centrale 5. Ponts avant et arrière 6. Sections de proue et de traverse 7. Revêtement et dérive en tissu 8. Moitié arrière du siège longitudinal 9. Sections de coque arrière
Nous n’avions jamais résolu le problème de l’étanchéité des joints de pliage, la solution était donc d’éviter complètement ce problème. Nous avons décidé de faire du tissu une peau qui s’asseoirait autour de la coque en contreplaqué, en utilisant de généreuses fléchettes dans le matériau pour obtenir de bons chevauchements. De cette façon, nous collerions simplement des morceaux de tissu plats ensemble, et cela est fait de manière fiable avec les colles en deux parties recommandées.
La construction a été retardée alors que nous avons déménagé, fuyant Londres vers la côte Est. Nous avons construit un atelier dans le jardin, mais les premières choses que nous avons construites là-bas étaient des portes de jardin, des bibliothèques, puis un dériveur rigide et un nouveau kayak à utiliser sur la rivière de l’autre côté de notre voie.
Le nouveau canot pliant a été conçu à nouveau comme un modèle en papier, puis, comme la coque a une forme simple, un tableur Excel a été utilisé pour vérifier le tirant d’eau (et donc le franc-bord).
Nous avons également calculé la position du centre de flottabilité avec différentes charges, car dans un dériveur léger, l’équipage doit pouvoir s’asseoir pour que le bateau soit équilibré. La solution la plus simple consiste à utiliser un siège longitudinal et à disposer de deux jeux de verrous. Avec deux personnes dans le bateau, les verrous avant sont utilisés et avec une ou trois personnes, l’ensemble arrière est utilisé.
La planification terminée, il était temps de commencer à construire. Les panneaux de coque ont été découpés en contreplaqué marin à trois plis de 3,8 mm acheté en ligne à Robbins Timber de Bristol.
Les articulations des charnières ont été faites en cousant les planches ensemble à l’aide de la ligne de pêche Ultima Seastrike avec une résistance à la rupture de 100 lb. La ligne passe à travers des trous de 2 mm de diamètre, à 5 mm des bords des panneaux et espacés de 25 mm le long des bords.
Un fil suit un zigzag le long des trous, et un second fil forme les croix en zigzagant dans la direction opposée. Nous avons donné au bois quelques couches de polyuréthane avant de coudre les panneaux ensemble, afin que le polyuréthane puisse sceller les bords des trous (du polyuréthane de qualité extérieure provenant d’un atelier de bricolage est suffisant pour le travail).
Le dériveur se brise en deux à peu près au milieu. Parce que le joint n’a pas besoin d’être étanche, nous fendons simplement la moitié arrière entre des manchons en contreplaqué fixés à l’intérieur et à l’extérieur de la moitié avant du bateau. Quatre petits loquets à bascule de base obtenus en ligne auprès de RS Components sécurisent les deux moitiés ensemble.
Pour maintenir les côtés du canot à l’extérieur, et aussi pour aider à soutenir le siège, nous avons une cloison au milieu du bateau. Nous le fixons avec un système utilisé dans tout le bateau: sur les panneaux latéraux, nous collons des morceaux de bois résineux de section carrée de 10 mm en laissant un espace dans lequel la cloison coulisse. Partout où nous avons collé des composants ensemble, nous les avons également percés et collés dans une cheville de 6 mm, pour renforcer encore le joint sans poids supplémentaire. La cloison est maintenue en place de chaque côté du bateau en passant une goupille de 6 mm à travers elle et le bois de section carrée. Ces broches ne se sont jamais cassées en cours d’utilisation.
Pour maximiser l’espace utilisable dans le dériveur, la proue est équarrie. Un panneau vertical en contreplaqué est collé à la plaque centrale au fond du bateau, pris en sandwich entre du bois de section carrée. Le bord avant de cette plaque a du bois de section carrée collé des deux côtés, vers le bas duquel la plaque d’arc peut glisser en position. La verticale soutient en partie le pont avant, qui se verrouille sur la plaque d’étrave et les côtés du bateau. Au moment où le pont a été tiré vers le bas par des clips à bascule, l’avant du bateau devient rigide. Le même système est utilisé à la poupe.
Le siège longitudinal est réalisé en deux pièces. Les extrémités sont fendues pour se connecter avec les deux verticales à chaque extrémité du bateau. Le centre du siège repose sur la cloison transversale et également sur deux autres plis verticaux, qui reposent sur la plaque centrale au fond du bateau, près de son milieu. Ces verticales sont exactement là où la planche centrale se plie le plus lorsque le bateau est déplié et ne peuvent donc pas être collées en position. Il doit y avoir une certaine flexibilité pour le mouvement, même s’il ne fait que quelques millimètres, par exemple en utilisant du bois de section carrée pour emprisonner la verticale dans une rainure.
Peau et skeg
Vient ensuite la peau imperméable du bateau. Nous avons utilisé du polyester enduit de PVC 560g / m² d’Attwoolls Manufacturing, collé avec un adhésif PVC Polymarine en deux parties. Notre drap mesurait 1,5 m de large, assez pour recouvrir le fond du bateau d’un seul tenant avec quelques fléchettes de couture. Il peut être coupé à l’aide de ciseaux domestiques et collé facilement et de manière fiable à l’aide de la colle en deux parties.
Tous les bords de la peau sont repliés et collés, pour donner une double épaisseur pour la résistance à la déchirure, et un cordon passe autour du bateau, à l’intérieur du pli, pour empêcher les bords de s’étirer.
Aux arcs, nous chevauchons la peau sur le pont avant et y glissons la structure en contreplaqué. Ce chevauchement renforce encore la structure de la proue. De même, à la poupe, un rabat dans la peau chevauche le pont arrière et est attaché à l’aide de la corde.
De chaque côté du bateau, il y a deux courtes longueurs de Velcro robuste, 50 mm de large, pour empêcher la peau de s’affaisser.
Le skeg est incorporé dans la peau. En coupe transversale, il a une forme en T avec la partie supérieure du T fixée à la peau par des bandes collées de la feuille de plastique. Pour plus de solidité, le skeg est fait d’un pli marin de 10 mm. Le tissu est suffisamment solide pour maintenir le skeg en place. En fait, nous n’avons eu aucune déchirure dans la peau en trois ans d’utilisation.
Utilisé en croisière
La coque pliée se range dans des sacs faits maison dans le local technique de notre Sirius 310. Chaque sac est suffisamment léger pour être facilement soulevé et transporté jusqu’au pont avant où la structure en contreplaqué est assemblée. Une drisse de rechange le soulève pour que nous puissions y glisser la peau, le dériveur est ensuite abaissé sur la drisse dans l’eau, et remorqué jusqu’à la poupe pour un accès facile. L’assemblage prend dix minutes.
Le dériveur a maintenant été utilisé lors de voyages au Danemark, en Norvège et sur la côte ouest de l’Écosse avec une usure minimale. Evidemment on fait attention lors de l’atterrissage sur une plage de galets, mais le dériveur est facilement transporté sur la plage par une personne à chaque extrémité. Il rame facilement et est stable – un adulte peut se tenir sur un côté sans le chavirer – et il remorque avec bonheur.
Ce bateau met l’accent sur son côté pratique et nous ne prétendons pas qu’il est beau. Mais malgré la longue genèse, sa construction et son utilisation ont donné beaucoup de plaisir.
[ad_2]